日本製造業の競争力の源泉は、現場班長の弛まないカイゼン力と言っても過言ではありません。
「現場で何が起きているのか?」日々見える化を重ね、品質向上と効率化に取り組んだ結晶として現在の繁栄があります。
今、製造業には新たな潮流としてデジタル化による産業革命が起きようとしております。
その中で、現場班長へ、より多角的な情報を提供することで、現場力向上をサポートします。
DX:デジタルトランスフォーメーションとデジタル化
デジタルトランスフォーメーション
将来の成長、競争力強化のために、
データとデジタル技術を活用し
新たなビジネス・モデルを創出・柔軟に変革する
テクノロジーとデータの活用によってビジネスモデルの変革を図るデジタルトランスフォーメーション(DX)の実現は、あらゆる業種で重要なミッションとなっています。製造業における“ものづくり”の現場にもDXの波は押し寄せており、多くの企業や製造現場で検討が始まりつつあります。
製造業におけるDXとは何か?どう進めるべきか?
DXの重要性を理解する企業は増えてきていますが、全社的な取り組みを進めている企業はごく少数です。
私たちはDXの実現に向けて、デジタル化をする必要があると考えています。
DX(デジタルトランスフォーメーション)、Digitalization(デジタル化)、Digitizaion(電子化)とキーワードがあります。電子化は文字通りデータを作り出すこと、デジタル化というのは電子化されたものがつなぎ合わせれて、一連のプロセスがデジタルの世界で可視化できる状態になるものです。
DXの実現に向けてまず取り組むべきはことは、生産の現場で起こっている、”コト”をデジタル化する、つまり、ヒト・設備の動きを生産の流れにあわせてデータとして収集にすることではないでしょうか。
IoTの活用
今までデータを取れなかったものも
すべてデータ化する プラットフォーム
IoTでリスクを回避
IoTについては、センサーの低価格化やデータ収集基盤をあわせたサービス提供など、より導入しやすいものが増えてきています。
また、最新の設備にはネットワーク接続できるものが標準化されてデータ収集がより進む環境が整備されつつあります。
しかし、実際の製造現場では稼働から何年も経過した設備をこれからも使い続ける必要があり、新しい設備をすぐに導入することができません。
現場のデジタル化を進める上では、新しい設備だけでなくこの古い設備についてもIoTでつなげることが重要になってきます。
最近ではレトロフィットIoTと呼ばれている内容です。
古い設備をIoT化するための方法は2通りあります。
1点目は、設備の電気信号を読み取る方法です。
これは設備とセンサーを物理的にケーブルで接続しデジタルデータに変換します。ただし、物理的につなぐことになるため、設備側の動きに影響が出る可能性があり、設備メーカーと会話できるIoTベンダーの選定が必要になります。
2点目は、設備の外側にセンサーを取り付けて動きを検知する方法です。
ライトの点灯を光センサーで検知したり、物の通過を赤外線センサーで検知したりします。この場合、正確に検知できるものもありますが、外側から検知することになるので、実際の設備の動きと少しずれる可能性があります。
すべてオートメーション化されている工場であれば設備のデータをIoTで収集することにより、デジタル化が進みます。
しかし、多くの工場はヒトが主役であり、ヒトも動きがわからないとその先に進めません。
設備の動きをIoTでヒトの動きをITを活用し収集することにより、プロセス全体をデジタル化することができ、今まで見えなかった現場の動きが見えるようになります。
ちなみに、現地・現実・現物という3現主義はIoTで置き換えられることはありません。
データをつなげる
現場で起きている“コト”をデジタル化
データはかけあわせ、つながることで見えてくる課題解決につながる
切断
どの品番を切断する時に設備が停止しやすいか?
設備×品番
溶接
熟練作業者と一般作業者での段取時間の違いは?
設備×ヒ ト
塗装
品番に最適な環境温度は?
品番×環境
組立
品番・ヒトごとに不良率がどれくらいあるか?
品番×ヒ ト
データは、“ヒト”ד設備”ד環境”דモノ”をかけあわせ、ものづくりの流れに沿ってつなぎあわせることで、カイゼン活動に大きな意味をもつデータに変わります。
実績班長はすべてのデータを収集し一元管理することで、現場のカイゼン活動を支援するのはもちろんのこと、多様な切り口での分析を可能にし、経営の迅速な意思決定も支援いたします。
加工組立業では、いつ、誰が、何を作っている時に、現場がどうなったか、が重要なデータであり、プロセス業では、ものづくりの環境と品質を作りこむための手順・動作が重要なデータになります。100社100様といわれる製造業の現場においては、必要なデータを必要な形でつなげて見ることができ、カイゼン活動につなげていけることが必要です。ただデジタル化を進めデータを取ることが目的ではなく、自社に必要なデータを取ることが求められます。
計量
品番をどの原料ロットでつくっているか?
設備×品番
混合
熟練者は現場でどのような調整をしているのか?
設備×ヒ ト
検査
品番と製造環境で不良率がどれくらい違うか?
品番×環境
充填
この段階の充填ロスがどれくらいか?
品番×ヒ ト
デジタルツインの世界
デジタルツインで
モニタリングとシミュレーションが可能に
現場のデジタル化を進めると、デジタルツインの実現に近づいていきます。
デジタルツインとは、直訳すると「デジタルの双子」を意味しますが、現実世界で起きていることをデジタルの世界で再現することです。
現実とデジタルでまったく同じ内容が再現されることから「ツイン(双子)」という呼び方をされます。
デジタルツインを実現することによって、現在得られる効果はなにか?
それは、モニタリングとシミュレーションの2点です。
モニタリングは、現実世界でも工夫を重ねて実現している、あんどん、生産管理版等が実現している見える化をデジタル上で表現することはもちろんのこと、今まで人の目では見えなかったことをデジタルを活用し可視化する効果もあります。
膨大なデータを解析した予兆検知、故障が発生した場合の迅速な原因の特定が実現できると言われています。
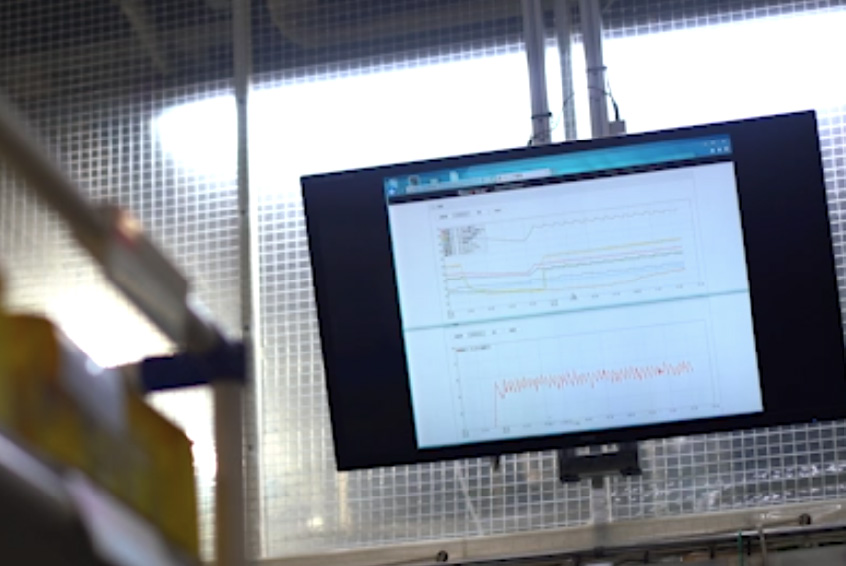
シミュレーション、それは、デジタル上で現実世界においてこれから起こる変化を予測する・できることです。ものづくりの最上流である設計では、従来よりCAD・CAEでのシミュレーションを活用していると思いますが、製造・保守の現場においても活用できるようになります。
生産ラインの組み換えや新設備導入により、現場にどのような効果・影響がでるか、何をどう作るといつ設備のメンテナンスが必要になるか、さらには販売後の利用されている現場の情報までデジタルツインで再現することができれば、設計で考慮する必要のないものが把握でき、製造工数や材料が減らすことによるコストの削減や、そもそも作る必要のない部品や加工を減らし品質向上が実現できる。デジタルツインにより今では考えられない効果を享受できる未来が見えてきます。
デジタルトランスフォーメーションの実現へ
デジタルトランスフォーメーションと
スマートファクトリー
ビジネスモデルの変革
製造業におけるデジタルトランスフォーメーションとは?
まず、デジタルツインを活用し生産を自動化していく流れ。つまりスマートファクトリーを実現する生産プロセスの変革。
次に、自社だけでなくサプライチェーン全体を巻き込み、AIを活用した需要予測とスマートファクトリーによる最適生産を組み合わせ、納期の劇的な短縮を実現し、さらに受注オペレーションと連携するような販売プロセスの変革。
最後に、販売後にお客様が使われている情報をもとに、製品設計を改良していく設計、そして保守部品の生産を調整する計画、そしてそれらを新製品の開発にフィードバックしていくマーケティングプロセスの変革があげられます。
スマートファクトリー実現までの流れ
DXにおける生産プロセスの変革は、経済産業省より提言されているスマートファクトリーを実現する、つまり上の図のレベル3:制御・最適化を実現することで、蓄積した知⾒・ノウハウや、構築したモデルによる 将来予測を基に最適な判断・実⾏ができる状況を指してします。
デジタル化で収集した大量のデータをAIの深層学習を用いてモデル化、リアルタイムに収集されるデータをモデルと比較し将来を予測、定められた目標から外れる傾向がわかると自動で現場を制御しあるべき姿に戻す。現実的には当面人間の判断が間に入り、その後、徐々にAIの判断による制御が導入されていくと予想されます。
DXへの取り組み
販売プロセスや設計・計画・マーケティングプロセスの変革については、経済産業省選定の「DX銘柄2020」に多数の事例が出ております。
製造業といっても販売のプロセスや保守サポートのプロセスは当然存在しますので、流通業や建設業といった異業種での取り組みも自社の業務を変革するためのヒントになる得るのではないでしょうか。